精密研削と超精密研削の特性と応用
研削によって達成できる精度は、生産開発につれて徐々に高くなりました。現在、研削精度により、通常研削(加工精度> 1μm、表面粗さRa0.16〜1.25μm)、精密研削(加工精度1〜0.5μm、表面粗さRa0.04〜1.25μm )、超精密研削(加工精度≤0.01μm、表面粗さRa≤0.01μm)に分けられます。
精密加工とは、一定発展期間に、加工精度、表面品質から高度な加工技術までを指し、今、加工精度L〜0.1µm、表面粗さ値Ra0.2〜0.01µmの加工部品を生産するテクノロジーです。
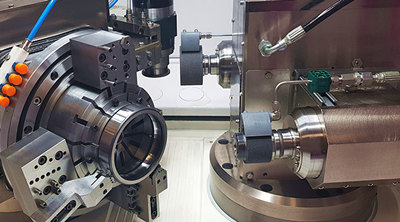
精密研削用超砥粒ホイール
現在、精密研削は、鉄鋼等の鉄金属や半導体等の脆性硬質材料の精密加工の主な手法の一つであり、現代の機械や電子機器の製造技術において非常に重要な役割を果たしています。
精密研削では、一般に、ダイヤモンドや立方晶窒化ホウ素等の高硬度砥石を使用します。主に砥石を細かくドレッシングし、ダイヤモンドドレッシングツールを使用して、小さく均一なマイクロフィード(10〜15mm /分)を行います。 マイクロエッジの後、加工面の研削トレースは細かく、最終的には非スパークライト研磨を採用します。
精密研削とは、精密研削盤で細粒砥石を選択し、砥石を細かくドレッシングすることで、マイクロエッジと等尺性を備えさせることです。 研削後、研削面に残る研削痕は非常に細かく、表面仕上げが良いです。
超精密研削とは、加工精度0.1μm以下、表面粗さ0.025μm未満の方法で、サブミクロンレベルの加工方法であり、鋼材、セラミック、ガラス等の加工に適し、今ナノメートルレベルに向かって発展しています。近年、超精密研削の開発は非常に速く、鏡面研削、マイクロ研削、高速研削等、超精密研削に関連する研削工程がいくつかあります。
1.精密および超精密研削の特徴:
(1)精密・超精密研削はシステムエンジニアリングです。
精密及び超精密研削はただの加工方法ではなく、システムエンジニアリングです。その構成部分は、被削材、精密・超精密研削機構、精密・超精密研削盤、ホイールとドレッシングツール、ワークピースの位置決めとクランプ、検出とエラー補正、作業環境、作業員のスキルが含まれていて、どれも欠かせないものです。 その中、精密・超精密研削盤は、加工精度を確保するための鍵です。
(2)超砥粒ホイールは精密・超精密研削の主な工具です。
砥層幅が極めて薄く、研削深さが非常に浅く、高温強度と高温圧力を備えた研磨材が必要です。そのため、ダイヤモンドと立方晶窒化ホウ素(CBN)の超硬質研磨剤を使用します。 表面粗さの要件が低いため、研削には超砥粒ホイールを使用しています。
(3)精密・超精密研削は、一種の超微細切削プロセスです。
精密・超精密研削は、結晶内部面の超微細研削で、除去される加工代は非常に小さく、ワークに求められる精度に達するための加工プロセスです。
2.精密及び超精密研削の適用
(1)鉄鋼とその他の金属材料、特に焼入れプロセス後の焼入れ鋼の研削。
(2)セラミック、ガラス、石英、半導体材料、石材等非金属の硬脆材料の研削。
(3)現在、外周、平面、いろんな穴の超微細研削に使う外周研削盤、平面研削盤、内面研削盤、座標研削盤等があります。
(4)精密研削、超精密研削とその自由な研磨処理は完備。